In the process of making optical filters, for coated filters, the degree of cleaning of the substrate determines the quality of the coated products. Ensuring the high cleanliness of optical components before coating is the most important step in the filter manufacturing process. The substrate needs to be cleaned before entering the coating to achieve degreasing, decontamination and dehydration, so as to effectively improve the firmness between the film layers.
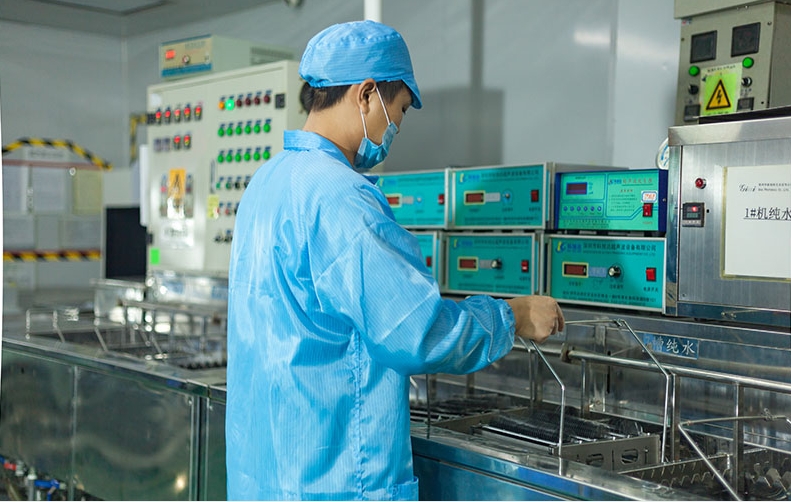
In the general cleaning industry, it is generally divided into wet cleaning and dry cleaning according to different cleaning agents. For the coated filter industry, the cleaning methods of the substrate before coating are generally divided into physical cleaning and chemical cleaning. Physical cleaning is to remove the attachments on the surface of the substrate, such as dust and dust. Chemical cleaning is to remove chemical attachments on the surface of the substrate, that is, oil stains. The following are four cleaning methods for optical filters!
Wiping cleaning
Generally, wiping cleaning has the best decontamination effect with both mechanical friction and chemical action. Before the filter is transferred to the coating process, it is generally equipped with ultrasonic cleaning for a few minutes before wiping cleaning, and then rinsed with ionized water for better effect.
After the substrate is polished, there may be some sticky particles and oil on the surface left after polishing, so before coating, the filter substrate needs to be soaked in acetone or other cleaning agents for a period of time, and then wiped with absorbent cotton. For example, base materials such as germanium, quartz, and sapphire are usually wiped with absorbent cotton dipped in acetone, and then wiped with absorbent cotton dipped in cleaning agent.
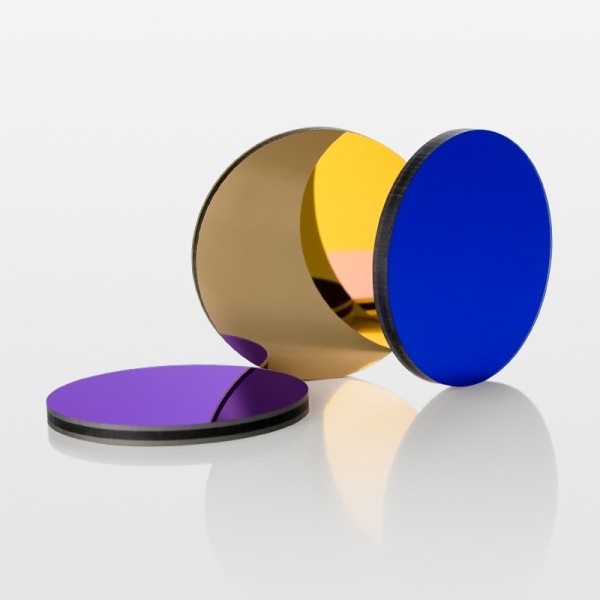
Ultrasonic cleaning
Ultrasonic cleaning generally uses ultrasonic cavitation, micro-acoustic flow generated by the second-order effect of ultrasonic cavitation for cleaning, and ultrasonic cavitation generates high-speed micro-flow at the solid-liquid interface for impact cleaning, thereby achieving high-speed, efficient and automated cleaning. The filter has high requirements for the surface cleanliness of the substrate before vacuum coating. Generally, different ultrasonic frequencies and different cleaning media need to be selected according to the type of pollutants. The cleaning frequency is generally in the range of 20-80k Hz. At the same time, the medium is heated. The cleaning medium can meet the conditions of selecting low tension, low ultrasonic attenuation, high grease solubility, harmless substances, etc., or select ionized water, neutral detergent, isopropyl alcohol, acetone, etc.
Vapor phase cleaning (steam cleaning)
Steam cleaning is also called organic solvent steam cleaning. It achieves the effect of cleaning the substrate to maintain high cleanliness by evaporating the organic solvent, liquefying and condensing it to the filter substrate, and dissolving the dirt. The cleaning tank of the steam cleaning device is heated and boiled by the organic solvent 141B to form a large amount of steam, so that the organic solvent steam in the upper space condenses and liquefies on the substrate, so that the dirt on the surface of the substrate is dissolved, and under the action of gravity, it flows down from the surface of the cleaned base into the liquid phase solvent along with the liquid containing dirt.
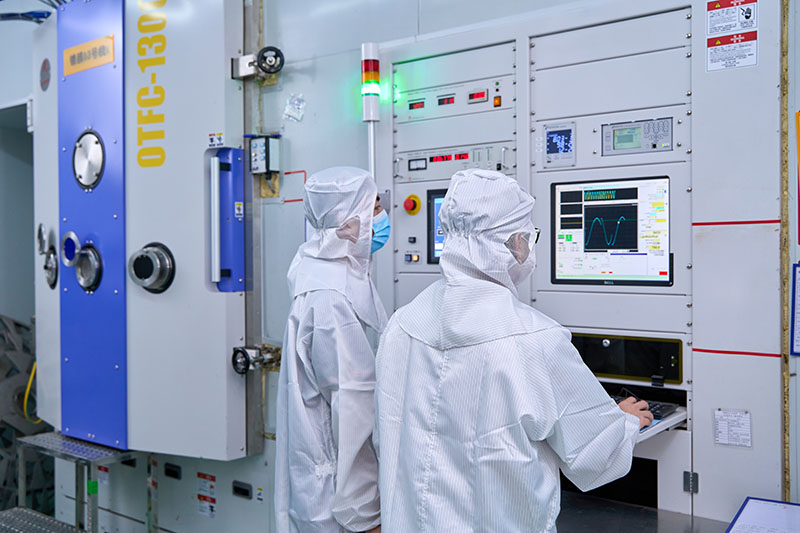
Ion beam cleaning
When the filter is transferred to the vacuum chamber process after cleaning before coating, there may be secondary contamination before the substrate is loaded into the vacuum chamber of the coating equipment and before evaporation. This process requires the substrate to be cleaned by the last ion beam. The principle of ion beam cleaning is to remove the dirt adsorbed or adhered to the substrate under the bombardment of high-energy ion beams or to oxidize the dirt molecules through high-heat oxygen ions so that the dirt can be separated from the substrate under ion collision.
The filter cleaning before coating is usually done by wiping and ultrasonic cleaning with different cleaning agents, then rinsed with deionized water and supplemented with vapor phase cleaning to meet the cleaning requirements before coating.