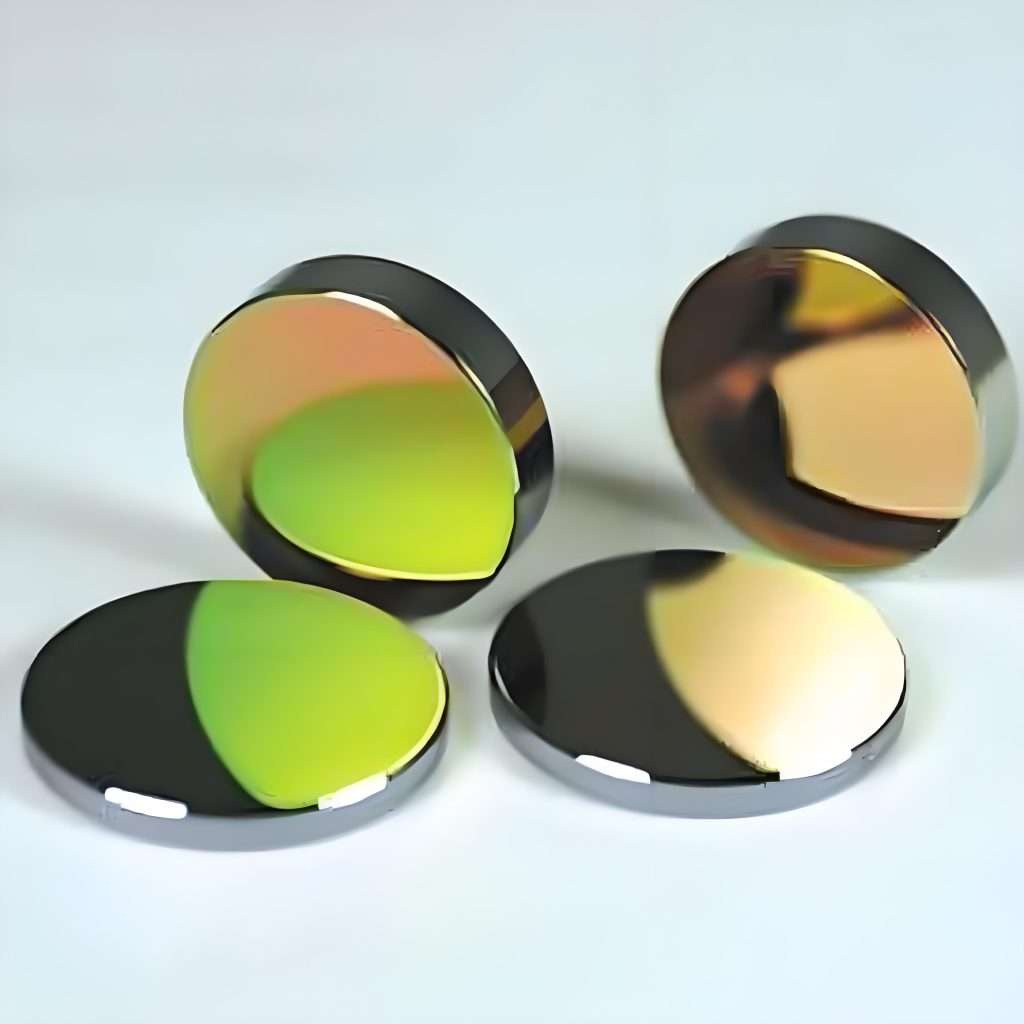
Molybdenum (Mo) has the characteristics of good high temperature strength, high hardness, high density, strong corrosion resistance, small thermal expansion coefficient, good electrical and thermal conductivity, etc. Molybdenum has extremely high surface strength and excellent heat dissipation effect. It is an ideal material for various harsh physical environments. Conventional molybdenum reflectors are uncoated products.
Model:Molybdenum mirror
Specifications: Customized
Material: Molybdenum
Features
1.High reflectivity: Molybdenum reflectors have extremely high reflectivity for light with a wavelength of 300~2000nm, with a reflectivity of more than 98%. When light hits the surface of the molybdenum reflector, most of the light will be reflected by the mirror instead of being absorbed or scattered. This high reflectivity makes molybdenum reflectors widely used in optical instruments, laser technology and other fields, and can effectively improve the utilization rate and transmission efficiency of light.
2.Corrosion resistance: Molybdenum reflectors have good corrosion resistance and can be used in humid and acidic environments.
3.Thermal stability and chemical stability: Molybdenum metal has a high melting point and can maintain stable performance under high temperature environments. At the same time, molybdenum has stable chemical properties and is not easy to react chemically with other substances. These characteristics enable molybdenum reflectors to maintain good working performance under harsh conditions such as high temperature and corrosive environment, and are suitable for various complex environments.
4.Mechanical strength: Molybdenum metal itself has high hardness and toughness, and can withstand greater pressure and impact. This makes the molybdenum reflector less likely to deform or damage when subjected to external forces, ensuring its reliability and durability during use.
5.Easy processing: Molybdenum reflectors are easy to process and can be processed into various shapes and sizes, suitable for manufacturing various optical devices.
Manufacturing process
The manufacturing process of molybdenum reflectors includes material preparation, molybdenum substrate processing, reflective layer preparation, reflective layer modulation and surface treatment.
Surface treatment: including coating a protective layer, applying an anti-reflective coating or performing optical film stacking to further improve the optical performance and durability of the molybdenum mirror.
1.Material preparation: Prepare the materials of the molybdenum substrate and the reflective layer. The molybdenum substrate is usually made of high-purity molybdenum sheets or molybdenum rods.
2.Molybdenum substrate processing: including steps such as cutting, grinding and polishing. First, according to the design requirements, the molybdenum substrate is cut into the required size and shape; then the molybdenum substrate is coarsely and finely ground using a grinding machine to obtain a flat surface; finally, the surface quality of the molybdenum substrate is further improved through the polishing process.
3.Reflective layer preparation: usually physical vapor deposition (PVD) or chemical vapor deposition (CVD) and other technologies are used. In the PVD process, the high-purity reflective material is heated to the evaporation temperature, and then the reflective material is deposited on the molybdenum substrate by evaporation or sputtering; in the CVD process, the reflective material source gas is introduced into the reaction chamber to deposit on the molybdenum substrate to form a reflective layer.
4.Reflective layer modulation: In order to obtain the desired optical properties, the reflective layer usually needs to be modulated. This can be achieved by controlling parameters such as temperature, gas flow and deposition time during the deposition process.
5.Surface treatment: including coating a protective layer, applying an anti-reflective coating or performing optical film stacking to further improve the optical performance and durability of the molybdenum mirror.
Applications
Microscopes: Used to separate excitation light and emission light of different wavelengths.
Spectrometers: Decompose composite light into monochromatic light.
Lasers: Used to combine or separate laser beams of different wavelengths.
Projection equipment: Combines light beams of different colors to form a color image.
Photographic equipment: Used to split light and improve image quality.
Medical equipment: Used to separate light of different wavelengths during surgery.
Stage lighting: Create colorful lighting effects.
mirror | |||||||
model | diameter | thickness | Angle of incidence | Base material | Coating | ||
mm | inch | mm | inch | ||||
GIAI-Mo-20-3 | 20 | 0.79 | 3 | 0.12 | 45 | molybdenum | none |
GIAI-Mo-25-3 | 25 | 0.98 | 3 | 0.12 | 45 | molybdenum | none |
GIAI-Mo-30-3 | 30 | 1.18 | 3 | 0.12 | 45 | molybdenum | none |
GIAI-Mo-38.1-5 | 38.1 | 1.5 | 5 | 0.2 | 46 | molybdenum | none |
GIAI-Mo-38.1-6 | 38.1 | 1.5 | 6 | 0.24 | 47 | molybdenum | none |
GIAI-Mo-50.8-5 | 50.8 | 2 | 5 | 0.2 | 48 | molybdenum | none |
GIAI-Mo-50.8-6 | 50.8 | 2 | 6 | 0.24 | 49 | molybdenum | none |
GIAI-Mo-76.1-6.35 | 76.1 | 3 | 6.35 | 0.25 | 50 | molybdenum | none |
GIAI-Mo-50.8-7.6 | 76.1 | 3 | 7.6 | 0.3 | 51 | molybdenum | none |
GIAI-Mo-76.1-10.2 | 76.1 | 3 | 10.2 | 0.4 | 52 | molybdenum | none |
GIAI-Mo101.6-10.2 | 101.6 | 4 | 10.2 | 0.4 | 53 | molybdenum | none |
Application areas
Laser system: High reflectivity lenses are needed in laser systems to increase the laser output power. Molybdenum reflective lenses are a widely used option.
Solar cells: In solar cells, molybdenum reflective lenses can improve the energy conversion efficiency of solar cells, so they are also used in the production of solar panels.
Protective glasses: Molybdenum reflective lenses have high reflectivity and transparency, so they can be used as lenses for protective glasses, which can protect the eyes and ensure a clear field of vision.
Reflectors: In some special industrial production environments, high reflectivity lenses are required for precision testing, and molybdenum reflective lenses are one of the first choices.